This section of the Guide identifies issues that need to be monitored during the placement and compaction operations of the AC pavement.
3.1 Design Features and Shape
The paved lane/shoulder width and location of the Safety EdgeSM break point should be
discussed and established prior to paving. The Safety EdgeSM can be constructed on the
unimproved or improved shoulder with the break point lining up directly over the existing
pavement edge or over any portion of the previously paved surface as shown in Figure 9.
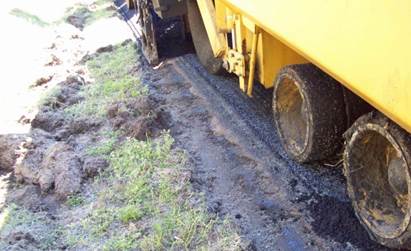
The intent is not to sacrifice paved lane/shoulder width to construct the Safety EdgeSM. Constructing the Safety EdgeSM onto the unimproved shoulder does not result in a decrease in paved lane/shoulder width.
The Safety EdgeSM is designed to create a 30 degree finished angle, relative to the pavement cross slope, on the edge of the pavement. Agency-specific tolerances may vary from those shown in Figure 10 which is from the FHWA guide specification. On projects where multiple AC layers are used, it is recommended each AC layer (except leveling layer) of the final 5 inches of AC receive the Safety EdgeSM as shown in Figure 10. For new construction or reconstruction with thicker AC layers, consideration should be given to widening the underlying paved layers to accommodate the Safety EdgeSM without decreasing lane width as shown in Figure 10. On projets with multiple AC layers, it is expected the additional volume of AC required to form the Safety EdgeSMwill increase bid quantities.
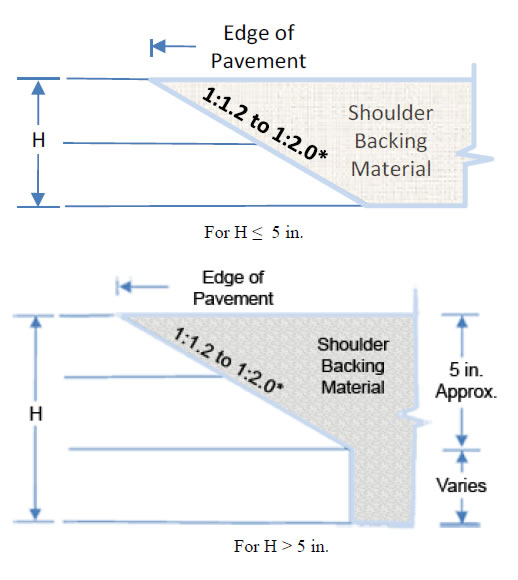
*Note, Recommended Rise to Run ratio range 1:1.2 to 1:2.0. The range of slope is equal to 26° to 40°.
3.2 Equipment – AC Safety EdgeSM Devices
The current commercial Safety EdgeSM devices can be grouped into two categories: (1) devices attached to the paver screed, and (2) modifications or attachments to the paver end plate. The devices listed below do not constitute an approved products list. Highway agencies should evaluate any new Safety EdgeSM hardware for compliance with specifications before approving for use on a project.
Devices Attached to the Screed
Currently, there are three devices available from two different manufacturers, which are: (1) the “Shoulder Wedge Maker” manufactured by TransTech, www.transtechsys.com and (2) the “Advant-Edger” and “Ramp Champ” manufactured by the Advant-Edge Paving Equipment LLC, www.advantedgepaving.com. Each manufacturer provides detailed installation instructions for attaching their devices to the paver screed. The devices can be easily attached to and removed from the paver screed with a simple two-bolt connection. The Safety EdgeSM device should fit closely to the end plate to prevent AC from getting between the device itself and end plate. The Ramp Champ can be set to a range of angles, while the other devices have a fixed angle.
End Plate Modifying Devices
The end plate modification devices are available from Carlson Paving Products, Inc. (Safety Edge End Gate) http://www.carlsonpavingproducts.com and Willow Designs LLC http://www.willowdesignsllc.com. The ski of the devices form the slope of the Safety EdgeSM and can be set to a range of angles. The screed operator can adjust the angle of the ski while paving to ensure the final angle of the Safety EdgeSM after rolling is close to 30 degrees.
3.3 Asphalt Concrete Materials
The Safety EdgeSM can be placed with all dense-graded AC materials that have been properly designed in accordance with existing mixture design methods, including: Hot Mix Asphalt (HMA), Warm Mix Asphalt (WMA), HMA with high amounts of Recycled Asphalt Pavement (RAP), HMA with Recycled Asphalt Shingles (RAS), polymer modified asphalt (PMA), rubberized gap graded and open graded mixes, and other specialty mixtures. The demonstration projects included HMA, RAP, RAS, WMA, and PMA mixtures.
There are two critical material issues in terms of placing a Safety EdgeSM for AC mixtures: (1) lateral movement of the AC mix during compaction and (2) the size or amount of coarse aggregate in the AC mixture.
- Most AC mixtures exhibit some lateral movement under the rollers during compaction and that movement is mixture and application dependent. Lateral movement of the AC mix should not prevent the contractor from achieving an acceptable Safety EdgeSM slope after final rolling. Ensure that after rolling is completed the Safety EdgeSM break point lines up directly over the existing pavement edge or over any portion of the previously paved surface. If the break point is over the unimproved shoulder (i.e. different support structure) the potential of a longitudinal crack forming is greater (Figure 11). This material related issue is discussed in more detail in Section 3.4 – Safety EdgeSM Construction, under Rolling.
- The maximum nominal size aggregate of the mixture or amount of coarse aggregate can affect the surface texture or appearance of the Safety EdgeSM and measurement of the slope. Fine-graded AC mixtures were observed to have a tighter surface appearance and texture along the edge. Rough surface texture makes the measurement of the slope more difficult to quantify – increasing variability in slope measurements.
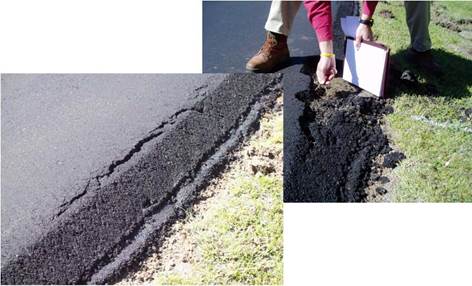
3.4 Safety EdgeSM Construction
This section discusses items of interest to asphalt paving projects when a Safety EdgeSM is to be placed as part of the new construction or rehabilitation project.
Safety EdgeSM Device Installation
Manufacturers of commercially available devices provide detailed instructions for attaching the Safety EdgeSM devices to the paver. Proper installation of the devices was discussed in a previous part of this section (Equipment – AC Safety EdgeSM Devices). A key issue for devices attached to the screed without guide rails is to ensure close installation to the end plate so loose mix does not get trapped between the device and end plate during paving operations. At the beginning of the day's production, when pulling off a transverse joint, the screed operator needs to monitor the position of the device as the auger chamber and extension are being charged to ensure the device is in contact with the end plate. These issues do not affect the end gate type device.
AC Placement
The Safety EdgeSM can be placed with normal paving procedures, and no changes to the operation of the paver need to be made. More importantly, the Safety EdgeSM device has no impact on how the paver operates, whether paving on an embankment or crushed stone layer, recently placed AC, existing AC or PCC layers, or milled surface.
For those agencies that require trial or control sections as part of standard AC paving operations, the slope of the Safety EdgeSM should be measured after all rolling has been completed to ensure the Safety EdgeSM slope did not "stand up" (substantial increase in the slope). Trial sections provide an opportunity for the screed operator to make adjustments to the Safety EdgeSM and screed before high production paving begins. For example, to obtain the 30o finished angle, the target angle to be achieved behind the paver by the Safety EdgeSM device may need to be shallower for a given mix, e.g., 25 degree. Trial sections can also be used to assess if the edge will "stand up" during the AC rolling operation. The issue of maintaining the slope of the Safety EdgeSM is discussed under the next subsection – Rolling.
The screed operator needs to watch and adjust three items during the paving operation when using a Safety EdgeSM device attached to the screed, described in Section 3.2: (1) the Safety EdgeSM device itself, (2) the end plate, and (3) the screed (refer to Figure 12). If the Safety EdgeSM device with too much downward pressure rides on the AC or other stiff base material that has been previously placed, this can result in undesirable paving results, as described below.
- When the Safety EdgeSM device rides on a base with a rough positive surface texture (e.g. coarse aggregate protruding upward such as in a chip seal) in some cases it may cause the screed to vibrate or jerk. The toe of the Safety EdgeSM can get caught on larger aggregate particles and when the particle breaks loose, the screed jerks. The screed operator will need to monitor the downward pressure of the Safety EdgeSM device so this does not happen in extreme cases.
- When the Safety EdgeSM device rides on a base with a varying longitudinal profile, the screed operator will need to monitor the downward pressure of the Safety EdgeSM device to keep the screed functioning as designed within the free-floating principle. The spring around the shaft of the Safety EdgeSM is designed to keep a relatively uniform pressure on the mixture being placed under the Safety EdgeSM – assuming the vertical operational limit of the Safety Edge is not exceeded.
- The screed operator also needs to monitor the downward pressure of the Safety EdgeSM device when it rides on soft surfaces. The leading edge of the device can dig into the soft shoulder pulling soil/aggregate into the asphalt wedge of the Safety EdgeSM. This is the same condition experienced in conventional paving when the paver end plate ski digs into the soft shoulder.
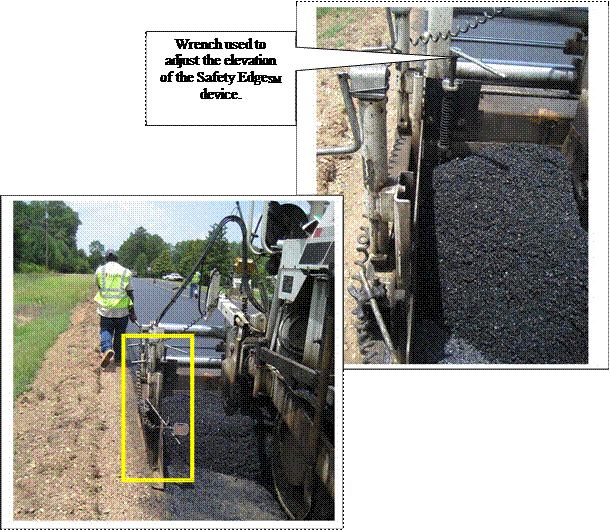
When paving begins the screed operator should pay close attention to the following items when using a Safety EdgeSM device attached to the screed.
- In charging the auger chamber with AC, the screed operator should ensure that the device is in close contact with the end plate so that mix does not get between the device and end plate and that there is sufficient material surrounding the device to keep it held against the end plate.
- After the paving operation begins and the full AC lift thickness has stabilized, the
screed operator should adjust the Safety EdgeSM device by lowering the device into contact with the underlying surface. This adjustment should not be made prior to the paver moving off the shims at the start of a day's paving operation. The screed operator should look behind the paver to ensure that the slope of the edge will produce a slope of about 30 degrees after rolling. - The paver end plate ski needs to remain in contact with the surface being paved over. AC can extrude out under the end plate ski if not in contact with the existing surface which can reduce the amount of AC available for the Safety EdgeSM – affecting the slope and density of the wedge itself.
- When placing an AC overlay, the Safety EdgeSM can ride on the underlying layer. However, the screed operator should closely monitor the downward force on the Safety EdgeSM device relative to underlying hard surfaces with variable longitudinal profiles, which can change the forces on one side of the screed (free floating screed principle or mode). This concern is heightened at intersections or areas of increased variation of longitudinal profile. The spring around the shaft of the Safety EdgeSM is designed to keep a relatively uniform pressure on the mixture being placed under the Safety EdgeSM – assuming the vertical operational limit of the Safety Edge is not exceeded.
- The operator needs to be aware that the height adjustment screw can be bent from paving with too much downward force, especially if the shoe is in contact with a variable elevation of a hard surface. The height adjustment screw can also be bent from or hitting objects while in transport.
- The screed operator should monitor the surface texture and condition of the Safety EdgeSM .
- When drawing in the hydraulic extension, the screed operator needs to closely monitor the process to ensure that the Safety EdgeSM device does not come in contact with the cross feed auger. If this occurs, it can damage both the Safety EdgeSM device and auger.
- If the hydraulic extension of the screed is extended during mainline paving, the amount of mix in the extension can be reduced near the paver end plate. When this occurs the screed operator should monitor the amount of mix to ensure it is not getting between the end plate and Safety EdgeSM device itself, as the screed moves out.
- The flow of AC material to the Safety EdgeSM device should be closely monitored to make sure enough material is available to form a continuous edge and that the material feed augers are properly positioned.
- Paver manufactures commonly recommend material feed augers be no greater than 18 inches from the end plate.
- When the paver is being moved, the Safety EdgeSM device should be removed or raised to its mounting height or uppermost position. This will ensure that the bottom of the device will not strike/get caught on any obstruction.
When using a Safety EdgeSM device the screed operator needs to continually be aware of the position of the break point of the Safety EdgeSM slope and keep the break point on the structural base or existing pavement.
At the beginning of the project, it is recommended that slope measurements be made immediately behind the paver and after each roller pass. The focus is on the final Safety EdgeSM slope angle after all rolling to determine how rolling impacts the final slope angle.
The contractor may want to periodically make these measurements as part of the quality control process.
Rolling
No special rollers are required for compacting the AC mix along and adjacent to the Safety EdgeSM (refer to Figure 13).
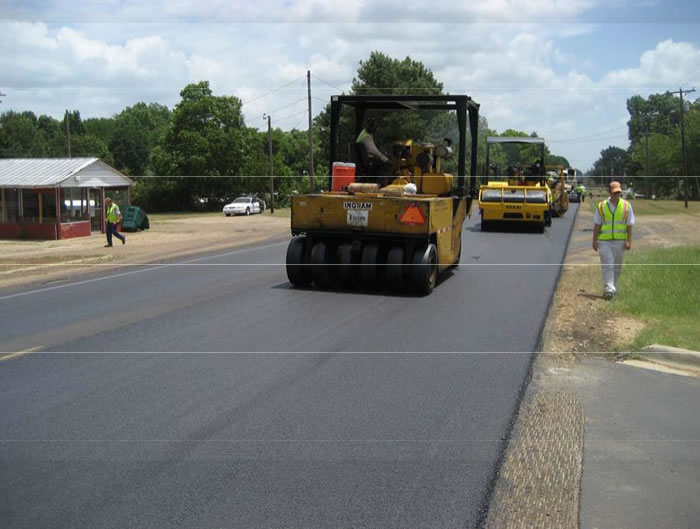
Most AC mixtures exhibit some lateral movement under the rollers during compaction. Lateral movement of the AC mix should not prevent the contractor from achieving an acceptable Safety EdgeSM slope after final rolling. For some of the demonstration projects, the contractor did change or revise the standard rolling pattern to maximize the density of the AC mat, while retaining an appropriate Safety EdgeSM angle. Just like for any AC paving project, the optimum rolling pattern is AC mixture specific. A rolling pattern used to compact a low stiffness mix and high stiffness mix may be different to meet the density requirements.
The following recommendations are made based on the findings from multiple demonstration projects.
-
-
- The contractor should roll the AC mat and pavement edges based on normal or standard compaction operation. This should ensure adequate density along and near the pavement edge. Multiple demonstration projects have been constructed successfully where the pavement edge was rolled with the contractor’s standard rolling pattern.
- After final rolling, the slope of the Safety EdgeSM should be measured. If the slope of the edge is too steep, the contractor should determine if the slope of the edge was steepened because of excessive rolling, the use of a mix that exhibits tenderness, or the AC mixture is simply too soft to retain the targeted slope angle. A variable angle Safety EdgeSM device can be used to place the Safety EdgeSM at an angle less than 30 degrees behind the paver, which should assist the contractor in achieving 30 degrees after rolling.
- Delaying the rolling of the edge of the mat should be the last resort taken to retain the slope of the Safety EdgeSM. This becomes a decision between durability along and near the pavement edge and retaining a slope of the Safety EdgeSM .
- Continually monitor the slope of the Safety EdgeSM after final rolling. The slope of the Safety EdgeSM varied between 30 to 40 degrees on multiple demonstration projects without delaying the rolling of the Safety EdgeSM.
-
3.5 Quality Measurement
The same properties used or identified by the owner agency to measure the quality of AC pavement layers for acceptance should also be used on projects that include the Safety EdgeSM. The acceptance plan should not be modified for projects that include the Safety EdgeSM. More importantly, the density, strength, and/or smoothness requirements appropriate for a typical project should not be relaxed simply because the Safety EdgeSM is added to a resurfacing or new construction project. Thus, the only difference between projects with and without the Safety EdgeSM is the slope of the edge itself.